e-TRNL Energy has raised INR 7.5Cr to build next generation cells with a unique 3D Electrode Architecture (3DEA) and manufacturing process that will make cells safer, cheaper, better and greener.
The increasingly urgent need to decarbonize the Earth hinges on electrification powered by renewable sources of power. Owing to the intermittent nature of renewable power, batteries are required to control the demand and supply of electricity. The global demand for batteries is expected to grow to upwards of 4TWh of storage by 2030, with electric mobility expected to be the main driver of the demand.
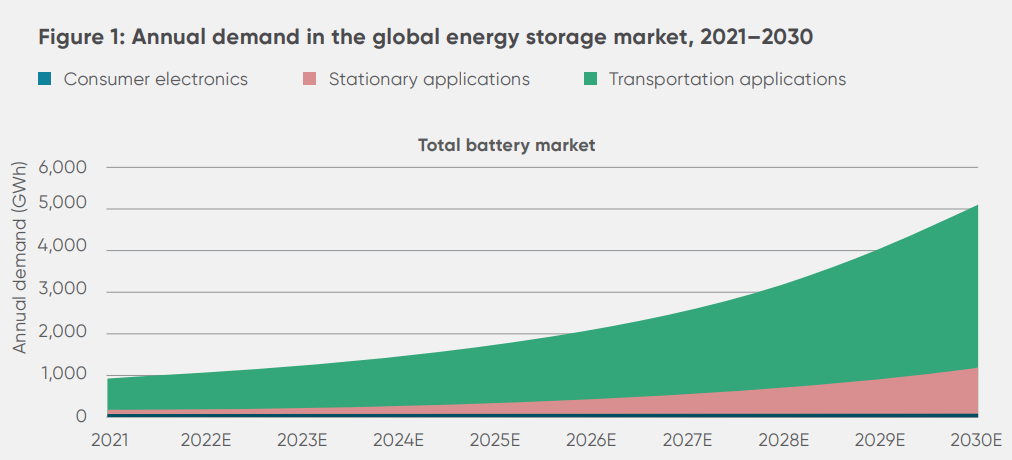
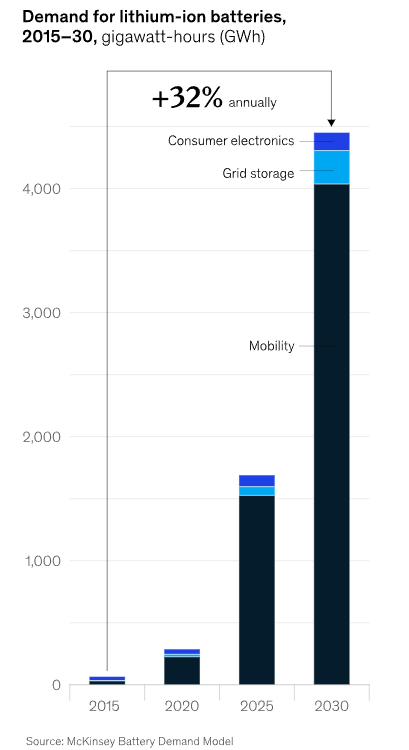
The batteries of today (dominated by Lithium Ion cells) however leave a lot to be desired. Slow charging times, limited range and cycle life, along with high costs and safety risks are holding back the rate of adoption of electric vehicles.
To solve this problem, the industry has explored multiple chemistries to optimize for the above factors. While NMC and NCA chemistries have seen wide adoption in EVs, LFP cells are steadily gaining more market acceptance, as witnessed by Tesla’s shift to LFP for a host of its models in 2021. A chemistry that solves for every need — range, safety, cycle-life and cost is still not a reality today.
At a component level, new materials for binders, current collectors, and innovative thermal management solutions have resulted in incremental improvements in battery performance and safety.
However, all these developments are hinged on the current architecture of the cells — a base material like copper and aluminum is coated with the anode and cathode materials respectively and then arranged in either a cylindrical or a prismatic manner. This design is primed to increase resistance to electron and ion flow and thereby, generate heat. And as the heat builds up, the cells become a safety hazard, while the range and cycle-life also go down.
Battery pack thermal management systems are employed to cool the cells. However, this solution counters the heat problem once the heat has been generated. What if we could construct the cell in such a manner that we could minimize/negate the heat generation in the first place.
It is this fundamental premise that Apoorv and Uttam chose to address. Together they have conceptualized a cell design — based around 3D Electrodes Architecture (3DEA) — that minimizes resistance and heat build-up, is chemistry-agnostic, and can solve for all that is lacking in the cells of today.
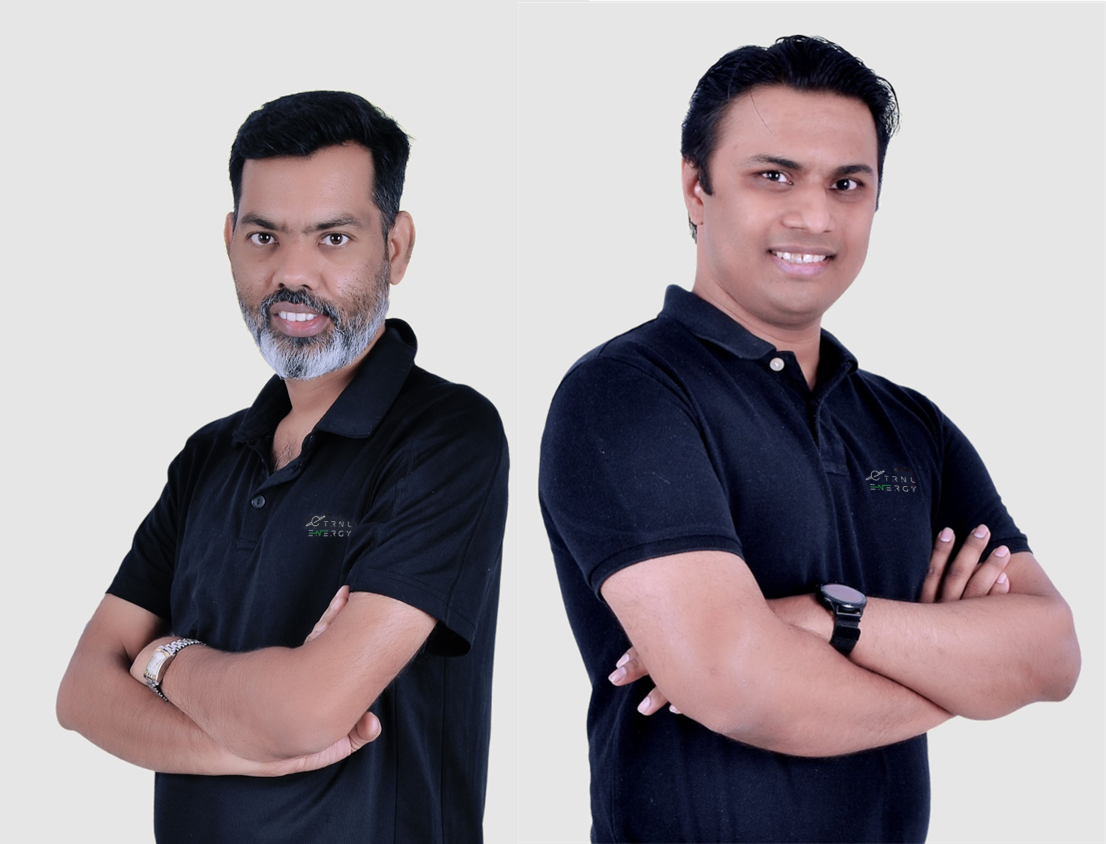
Having worked together at IIT-Bombay in the early 2010s, the two were among the first battery engineers at Ather Energy. During their time there, they set up a cell fabrication lab and built some of the first cylindrical Li-ion cells in India. Having spent more than a dozen years each in the battery space, the two come with an in-depth understanding of battery technology.
The less talked about problem in batteries is the manufacturing of these cells. The conventional process is
- Complex, involving expensive machines and high levels of quality control
- Difficult to repeat, with rejection rates in battery manufacturing usually around 5%, with some individual processes having high one-digit % rejection rates. The coating process, integral to all cell manufacturing today, sees the highest rejection rates of all.
- CapEx and OpEx Intensive, requiring large floor space, controlled temperature environments, clean rooms, safety cautions for personnel etc.
Further, a third of the cost of electrode production is contributed by two processes — Slurry mixing and Coating & drying. This amounts to 25% of the overall cell production cost and 6% of the overall cell cost.
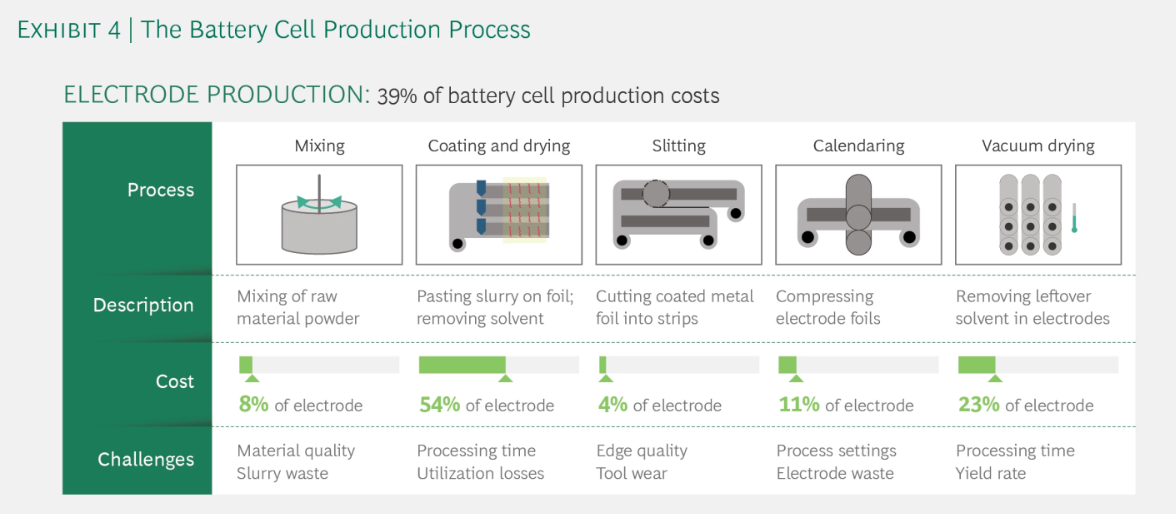
e-TRNL’s novel manufacturing process would reduce the number of steps by half, reduce the plant CapEx to 1/5th of a traditional plant, and cut down on the required OpEx. This ensures better repeatability and hence the likelihood of one cell being the same as the other increases.
Global tailwinds are blowing in the same direction. Tesla, the global leader in commercial cell technology, at Battery Day 2020 emphasized heavily on the innovations of tabless battery (architecture) and the dry-electrode process (manufacturing). In their quest to reduce the $/kWh by 56%, Tesla has outlined cell design and manufacturing as major focus areas, together contributing to 32% of the reduction.
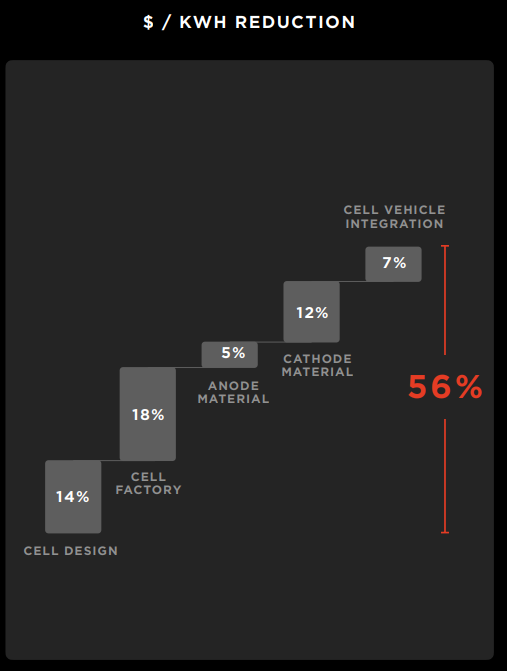
Traditionally, manufacturing cells is a gargantuan task and a low-margin business even at scale. It is also something that has never been attempted at scale in India. The lack of the supply chain and a cell manufacturing ecosystem only adds more complexity to the challenge.
In our conversations with potential customers of these cells — auto OEMs and battery pack manufacturers — two major themes emerged — one, an increased willingness to buy cells made in India as long as they offered superior performance, and two, a unanimous willingness to pay a premium for such cells. We’ve had our own portfolio companies affirm these sentiments.
When we at Speciale started to build our thesis on cell technologies, a few things became clear to us -
- A novel battery chemistry demands extensive R&D, time, expertise and resources. It usually begins as academic research, which then makes its way into the industry via an OEM.
- There is no one single battery chemistry that would solve all the requirements. Hence focussing on any one specific chemistry would reduce the TAM. A chemistry-agnostic solution would bring in greater opportunities for commercialization.
- Components such as binders, separators and coatings are drop-in solutions to the current processes, but cathodes and anodes face a tougher integration challenge.
- Thermal management solutions and battery management & analytics solutions are helpful, but do not tackle the core problem.
- Commercial viability is all that matters — The ability for a technology to work in the real world (beyond the laboratory) is the only thing that matters to partners, investors, and consumers.
- Indian battery startup ecosystem appears to be prioritizing (from high to low) the following: Charging infra > BMS Technology > Thermal Management > Recycling > Battery Chemistry (Li — ion improvements, Sodium, Zinc based batteries) > Raw Materials
Innovations in battery architecture and manufacturing processes fall under a category of innovation that requires ‘substantial modification and/or the addition of novel process steps for component production and/or cell assembly’
While these are still early days in e-TRNL’s journey, our conviction was largely driven by,
- the fundamental, ground-up nature of innovation to a complex global problem, and the large scale impact that it can have
- an incredible team that has a deep understanding of the battery value chain
- faster path to commercialization compared to traditional cells
- encouraging responses from potential customers
The fundraise will help e-TRNL set up their lab facilities, manufacture the first prototype cells and pilot them on two wheelers. This will set the course to achieve $100/kWh by 2025 — considered the global inflection point to drive widespread adoption of EVs over ICE vehicles.
We are thankful to our co-investors — Micelio Mobility and CIIE for their conviction in e-TRNL Energy. We are thrilled to partner with Apoorv and Uttam as they spearhead the development of a path-breaking cell design out of India.
To join the e-TRNL team, check out open roles here
Apoorv’s Medium page on all things batteries can be read here
_________________________________________________________________
We at Speciale Invest believe in supporting breakthrough technologies that have the potential to solve global problems.
As early stage investors, we like to get our hands dirty early on and support founders in their zero to one journey with patient capital, business development opportunities and hiring. We enjoy and thrive in the risk that comes with backing deep-tech startups at the pre-product stage and help through product-market fit, early customers and scale-up.
Climate Tech is a major investment theme across our $40M fund as we look to support the global decarbonization effort. Having made investments across Water, Green Hydrogen, Batteries, we are constantly on the lookout for stellar founders building solutions for Carbon Capture, HVAC, Motors, Sustainable Materials, Bio Fuels and many more.
Please do write to us at info@specialeinvest.com
To know more about Speciale’s investments in disruptive technologies, please check our portfolio