The fundamental rule in venture capital is to double down on the winners in your portfolio. This is why we chose to co-lead the $4.5M pre-series A round in CynLr and continue to support them in their vision to disrupt how products are manufactured. The funding enables the team to continue their pilots in auto OEMs and component suppliers and expand overseas.
Machines that relieve humans of repetitive/dangerous/heavy tasks have been around since ancient times. Modern robots find their origins in the 1950s and were initially imagined to assist humans as house helpers, loading the dishwasher and mixing martinis. But, technological limitations — size, function, safety — all prevented robots from mingling with everyday life, and hence, in the 60s, they quickly found their space on the factory floor..
Such Industrial Robots were fixed machines capable of carrying out manufacturing tasks which allowed production with less human work. Significant global technological developments over the past two decades in artificial intelligence, machine learning, telecommunication, IoT, machine vision, motors and actuators have all made robots more versatile, safe and collaborative with humans. As a result, robotics moved beyond manufacturing into farms, rescue sites, hospitals, laboratories etc.
Industrial Robots clocked in over $50 Billion in revenue in 2021. The number of robot deployments is only increasing — expected to grow by 13% for the next few years.
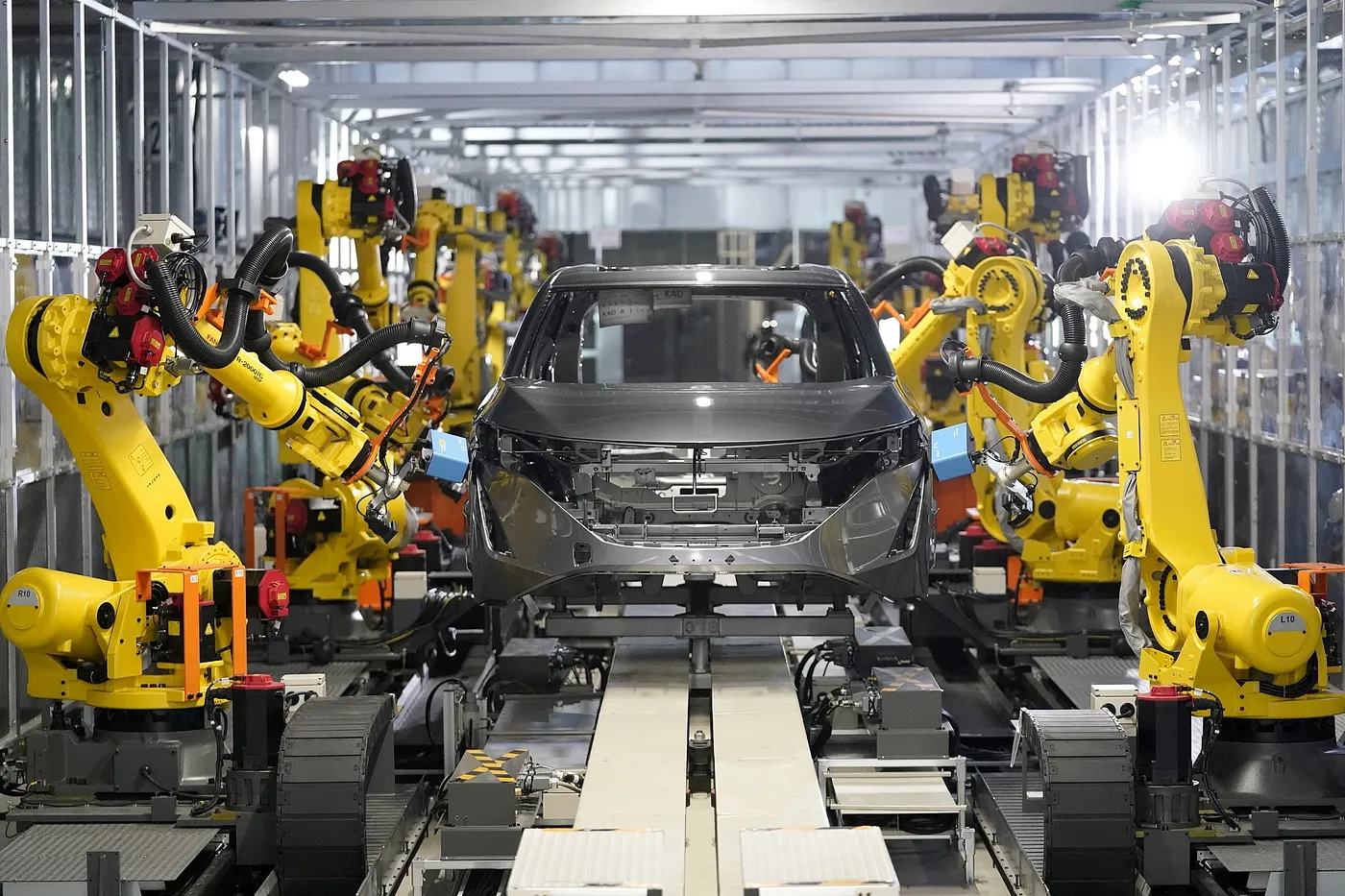
However, fluctuating customer preferences have resulted in a global shift towards high mix, low volume production in shorter cycles — calling for flexibility and agility in manufacturing. This comes at a cost. Tech Crunch’s 2016 piece on ‘The real cost of robotics’ qualitatively outlines the challenges of installing robots in a production facility.
TL; DR:
- It is complex. There are many moving parts — a robotic arm, a custom-built pedestal for it to sit on, a safety cage, end effectors (gripper — 2/3/4/5 fingered, process tools — screwdrivers, weld guns, paint sprays etc), tool changer, vision cameras, fixtures to hold parts and finally, the software that tells these robots what to do.
- It is expensive. Robotic arms and the additional attachments each cost thousands and sometimes, even hundreds of thousands of dollars.
These complexities and expenses still do not solve the two biggest drawbacks of industrial robots -
1. Robots are dumb, for the most part.
Humans (even babies) know how to pick objects, irrespective of how they are placed or oriented. They also know how much pressure to apply to hold these objects. But even after decades of commercial deployments, robotic arms cannot mimic this.
Robots operate best in closed environments and can do only tasks they are trained to do. Most robots today cannot pick up a part if it is not kept in the same position and orientation the robot was trained in. If your phone is placed as much as a few centimetres away or about 10 degrees at a different angle on a table, the robot cannot pick it up. The arm is not clever enough to realize that the position of the screw hole is off by 2 cms and hence, it has to reorient itself to place the screw in the hole. Pick, Orient and Place is a major challenge.
And as a result,
2. Robots lack flexibility
Robots that are deployed in industrial settings are usually static and carry out a single repetitive task. Production lines are designed, built and operated (at the cost of hundreds of thousands of dollars) mostly to handle just one product. For every new product, the line has to be repurposed. The robot cannot shift from picking up a screw to picking up a bolt overnight. It needs to be trained to do so and this takes time.
Put simply, this means that, a Toyota Innova cannot be assembled in the same production line as a Toyota Corolla because the line is purpose-built for the components and dimensions of an Innova.
CynLr is on course to address these challenges by reimagining how robotic arms function.
CynLr’s visual intelligence layer gives human-eye like capabilities to industrial robotic arms. The ability to pick up a particular object from a random pile is a problem that the world has long struggled to solve. CynLr’s hardware and software platform will enable robotic arms to pick, orient and place objects — from any position and orientation, just like humans do. This gives the arm a level of flexibility that has previously not been possible.
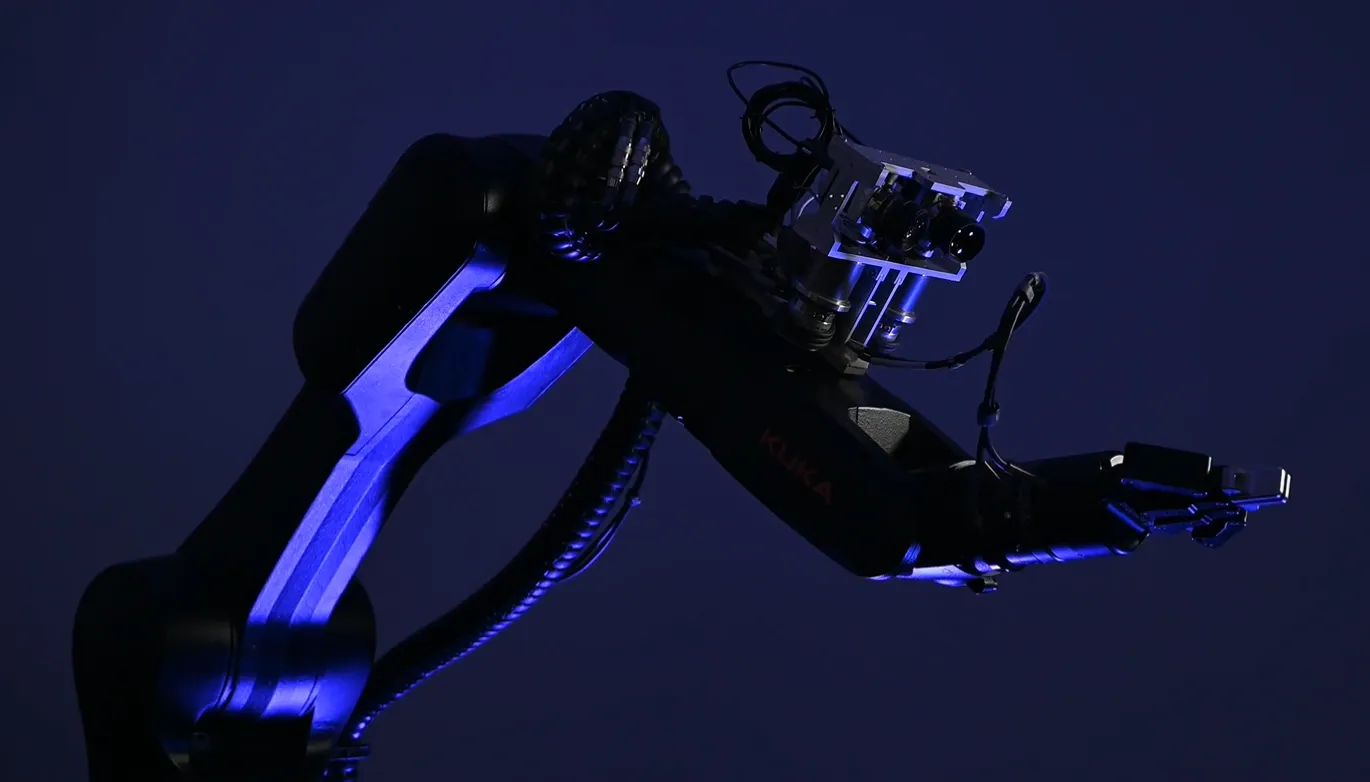
This foundational shift in how robotic arms function takes us one step closer to universal factories — product-agnostic lines where a line of robots can put together a printer today and a 2-wheeler tomorrow — with only simple reprogramming and retraining of the robots. Multiple products can be manufactured in the same line under the same roof, saving industries time and thousands of dollars in re-purposing.
We believe Nikhil Ramaswamy, Gokul N.A and the team at CynLr are determined to revolutionize how the manufacturing sector has been functioning for decades. When we first met them, we saw two passionate individuals who had spent close to a decade — first at National Instruments and then as consultants, solving automation problems for multi-national OEMs by leveraging AI and machine vision. Their profound understanding of the pain points in the manufacturing sector helped them identify the gaps and then envision a technology that could solve them.
As the first investors in CynLr back in 2019, we have seen their growth from being a small team testing the idea, to having built a working prototype and now running pilots with OEMs. In their discipline, attention to detail, and growth mindset, they have the fundamental ingredients to build a long-term institution at CynLr.
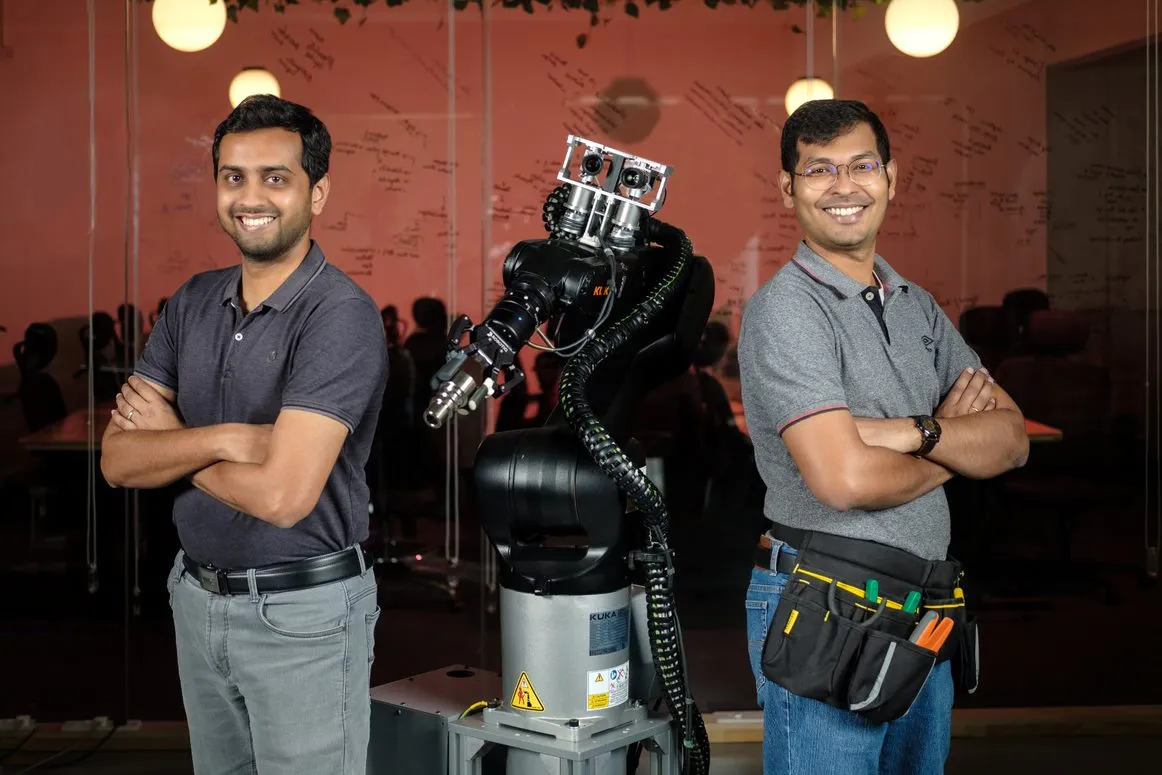
The $4.5M fundraise will help accelerate the team’s business expansion plans, see them deploy their solutions at a commercial level and clock revenues of the order of hundreds of thousands of dollars.
At Speciale, we have an unquenching thirst to back visionary founders who seek to disrupt the world as we know it today. We like to get our hands dirty early on and support founders in their zero to one journey with patient capital, business development opportunities and hiring. We enjoy and thrive in the uncertainty that comes with backing deep-tech startups at the early stages and watching them scale to new heights.
Our continued conviction in CynLr is a testament to our investment philosophy and we are super excited to have a front-row seat and support Nikhil and Gokul as they break into new frontiers.
To join the incredible team at CynLr, check out open roles here
You can also listen to Nikhil and Gokul share the CynLr story here and here.
To know more about Speciale’s investments in disruptive technologies, please check our portfolio